Oklahoma native Nick Morgan uses time-tested, ancient practices to handcraft primitive hunting bows.
It’s no surprise to those who know Morgan that he would discover a passion for creating traditional bows; he was an avid Robin Hood fan during childhood, and this arrow-wielding hero became Morgan’s primary inspiration.
“Whenever I start something, I always try to be the best,” Morgan says. “So right away, I became obsessed. I threw myself into bow making.”
While browsing YouTube looking for informational videos, the then 20-year-old Morgan stumbled upon an interview with Ed Scott. Well known in the bowyer community and largely considered one of the best bowyers of his time, Scott died in 2015 – but his videos struck an inspirational chord with Morgan. Fast forward to college at Oklahoma State University-Tulsa, (where Morgan graduated in 2013). He had some money left over from a scholarship, and, wanting to make the most of the money, he signed up for private classes with Scott in Grants, New Mexico. Morgan’s training in the craft for the previous three years came to reflect the familial relationship between teacher and student common in many of the cultures where bow making originated.
“I got really close with Ed. He became like a second grandfather to me,” Morgan says. “He imparted so much knowledge to me.”
Scott taught Morgan to make wooden, sinew-back, horn-belly bows. Taking his methods from tried-and-true Native American processes, Morgan uses mostly natural materials including sinew, which is processed animal tendons, and horn to make a fast-shooting hunting bow.
“Sinew is a pretty remarkable material,” Morgan says. “Indians figured out that animal tendon is very strong. They are weight-for-weight stronger than steel and 10 times more elastic than wood.”
The process to incorporate sinew onto the back of a bow takes months to complete, but the end result, Morgan says, is a strong, lightweight, silent bow that can last a lifetime.
“Clearly these bows work or they wouldn’t still be around,” he says. “It is so nice to go back to something so simple: a stick and string.”
“I don’t keep an inventory. I make each bow custom for my clients,” Morgan says. “Using sinew, you can make shorter bows and still get the proper pull back. When compared to a compound bow [with a levering system of pulleys and cables], a primitive bow weighs maybe a pound and makes no noise when you shoot them.”
Ancient bowyers were limited to natural materials immediately available to them, but Morgan takes advantage of traditional bow-making materials from around the world to improve his products. He strategically uses horn from the gemsbok, an African antelope, to the belly of his bows, giving them added compression strength without increasing the weight too much.
“I am always trying to make a better bow, and small details matter when you are making a high-end bow,” Morgan says. “I have lost years worth of work in some of my failures, but I learn a lot.”
The natural materials also present themselves with intricate appeal in additional to their functionality.
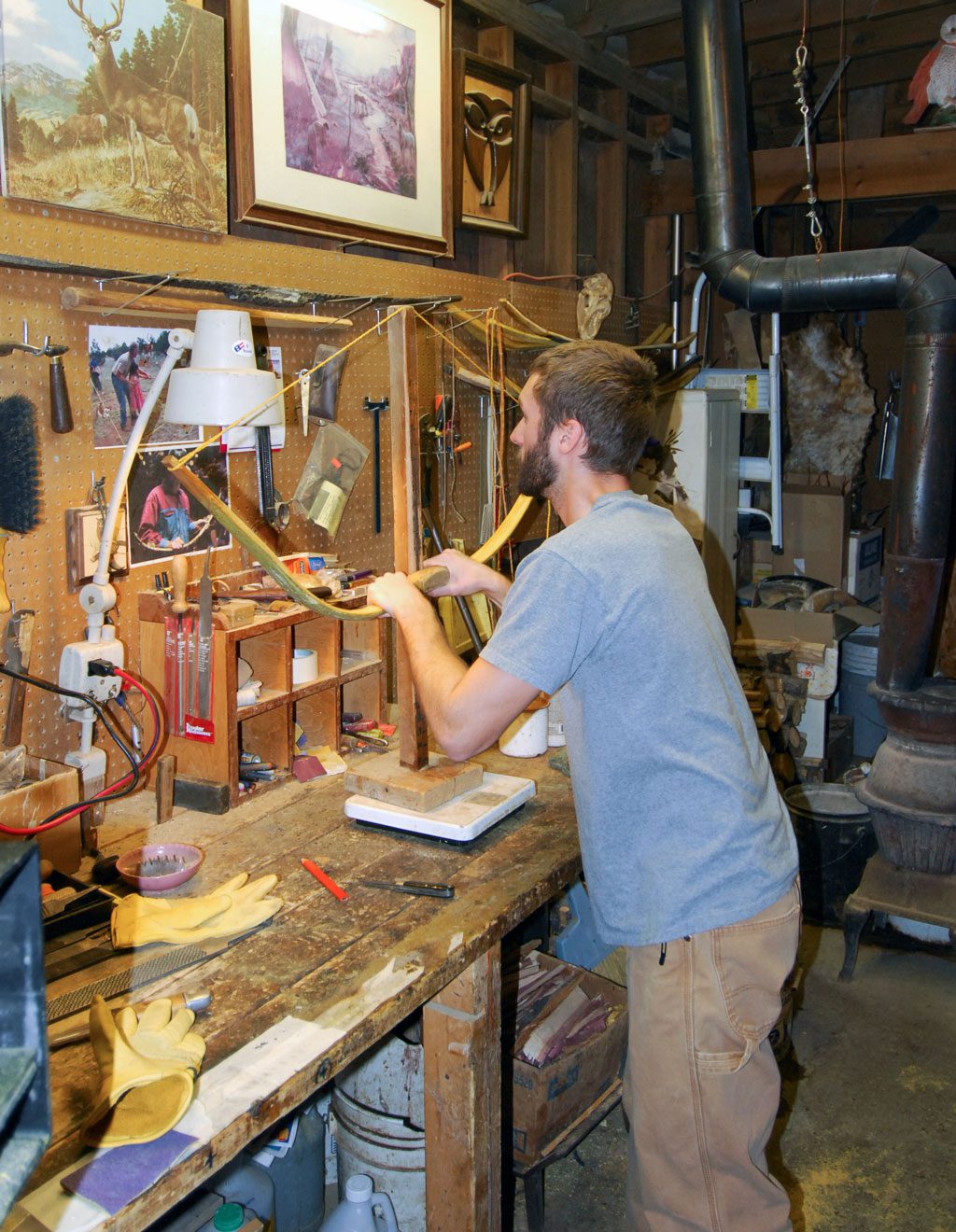
“If people are spending the money on my bows, I want to give them a high quality product,” Morgan says. “I want to give my bows every advantage I can to last a lifetime.”
Morgan puts in a lot effort to craft what he calls “the Ferrari of primitive bows.” Shooting one takes some practice, too.
“You have to be unbelievably focused if you want to shoot well,” Morgan says. “Focus is an important muscle to practice.”
For requests, Morgan can be reached at facebook.com/morganbows.